The boom in made in China is reflected not only in the surge in real estate infrastructure, but also in increased demand for elevators and accessories. Elevator manufacturing and elevator parts industry are ushering in a new stage of development. The contradiction between the growing demand for equipment and the outdated production technology has become increasingly prominent. with the development of science and technology, laser cutting technology is widely used in many industries, so is the elevator manufacturing industry.
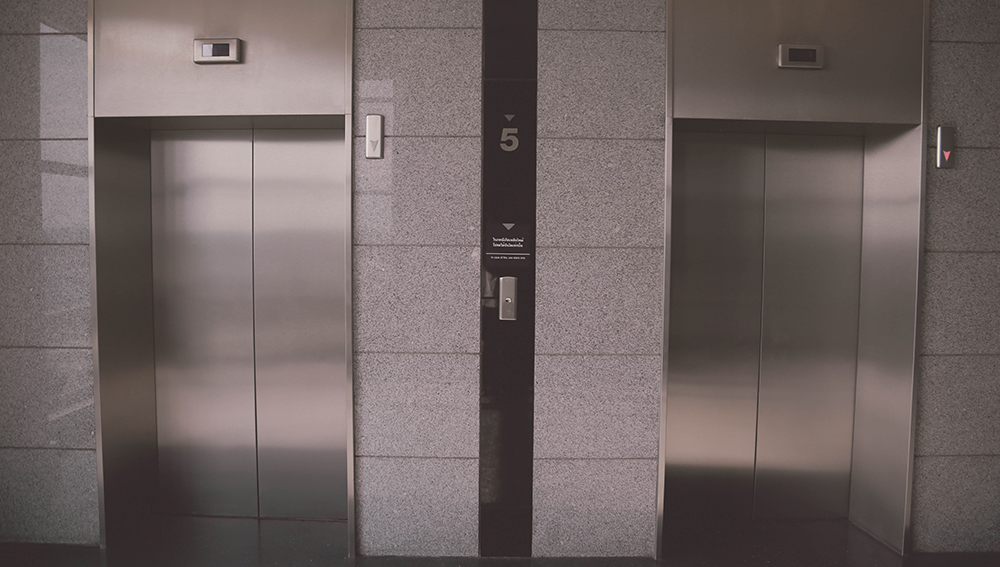
In the 1990s, elevator parts basically use multi-station stamping to process plates. Now, for safety reasons, elevator parts are basically made of metal. The development trend of elevator is mainly high-speed elevator technology, intelligent control and high efficiency of cleaning. With the emergence of several world-famous brands of elevators, imported laser cutting machines were introduced into domestic wholly-owned or joint ventures, and later laser cutting machines began to be used in the domestic elevator industry. With the emergence of domestic laser cutting equipment manufacturers, the situation that laser equipment can only rely on imports is broken, and it is put into use in the elevator manufacturing industry, which reduces the expensive price of elevators a lot. So domestic elevator companies and accessories companies have chosen to purchase laser cutting machines for production.
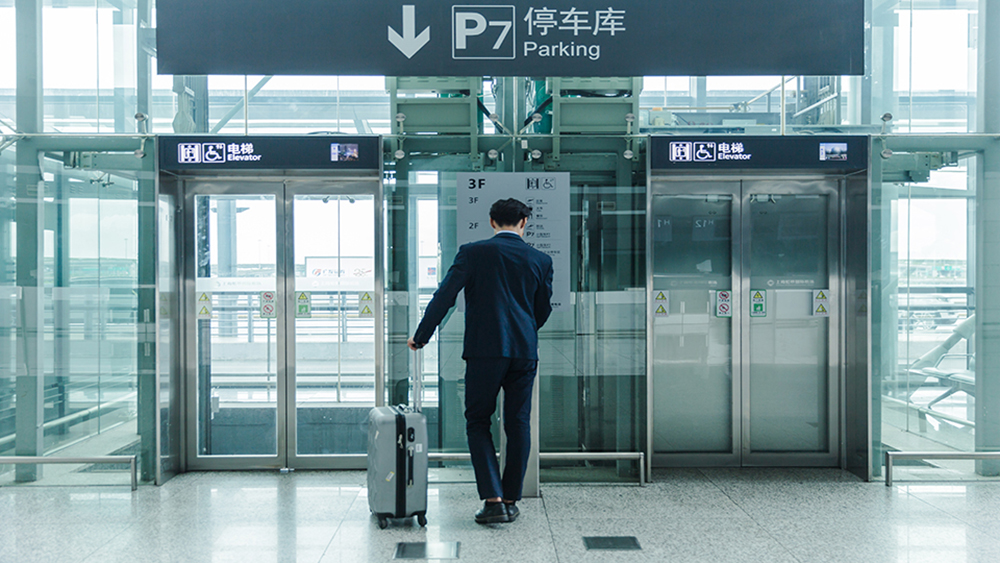
Taking elevator sheet metal processing as an example, more and more manufacturers choose laser cutting machine as the primary productivity to process fish-shaped plates, elevator door panels, escalators and supporting doors in elevator sheet metal manufacturing. In the past, the elevator sheet metal processing involves the mold design, the mold design is complex, the production takes a long period, very laborious, and the economic cost is also very high. therefore, at present, most companies will use laser cutting machines to complete the processing of elevator sheet metal, because the laser cutting machine will not be limited by the mold, and the scope and form of cutting are very flexible, even if there is no mold, we can achieve high-speed cutting of sheet metal. The processing time is greatly shortened and the processing cost is reduced.
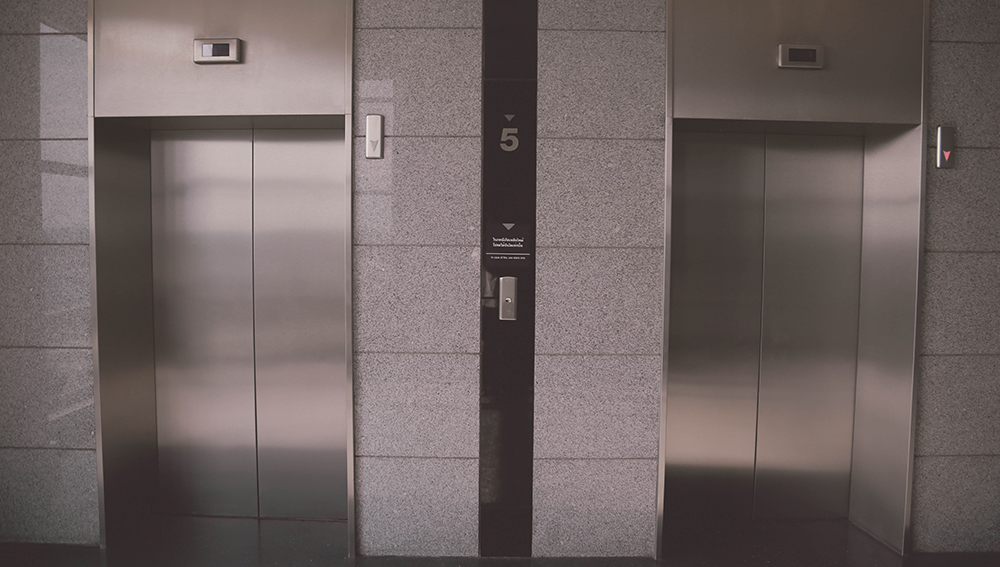
In the 1990s, elevator parts basically use multi-station stamping to process plates. Now, for safety reasons, elevator parts are basically made of metal. The development trend of elevator is mainly high-speed elevator technology, intelligent control and high efficiency of cleaning. With the emergence of several world-famous brands of elevators, imported laser cutting machines were introduced into domestic wholly-owned or joint ventures, and later laser cutting machines began to be used in the domestic elevator industry. With the emergence of domestic laser cutting equipment manufacturers, the situation that laser equipment can only rely on imports is broken, and it is put into use in the elevator manufacturing industry, which reduces the expensive price of elevators a lot. So domestic elevator companies and accessories companies have chosen to purchase laser cutting machines for production.
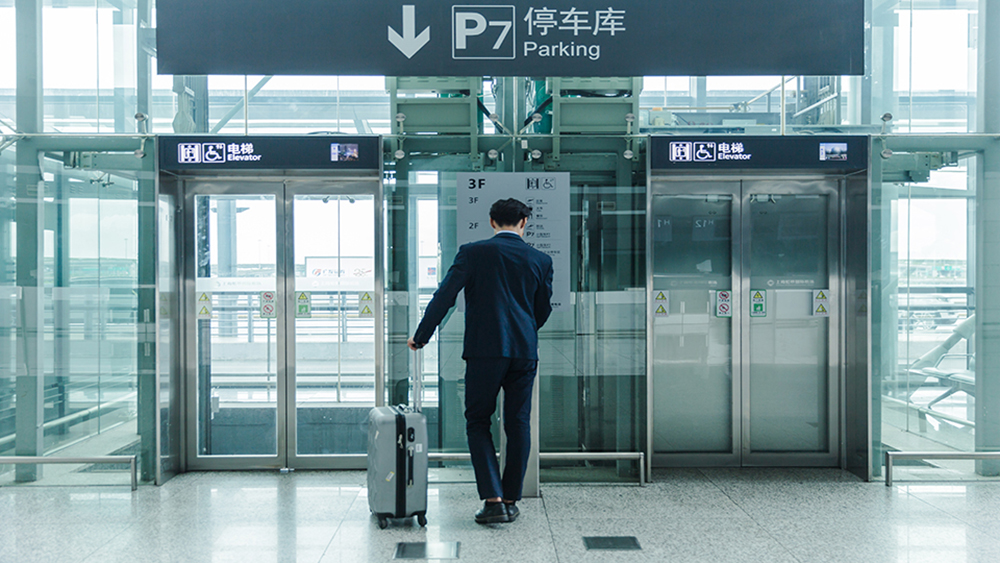
Taking elevator sheet metal processing as an example, more and more manufacturers choose laser cutting machine as the primary productivity to process fish-shaped plates, elevator door panels, escalators and supporting doors in elevator sheet metal manufacturing. In the past, the elevator sheet metal processing involves the mold design, the mold design is complex, the production takes a long period, very laborious, and the economic cost is also very high. therefore, at present, most companies will use laser cutting machines to complete the processing of elevator sheet metal, because the laser cutting machine will not be limited by the mold, and the scope and form of cutting are very flexible, even if there is no mold, we can achieve high-speed cutting of sheet metal. The processing time is greatly shortened and the processing cost is reduced.